图书介绍
飞机金属结构复合材料修理技术【2025|PDF下载-Epub版本|mobi电子书|kindle百度云盘下载】
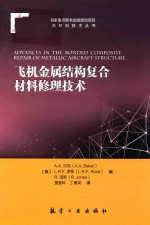
- (澳)A.A.贝克(A.A.Baker),L.R.F.罗斯(L.R.F.Rose),R.琼斯著;董登科,丁惠梁译 著
- 出版社: 北京:航空工业出版社
- ISBN:9787516512210
- 出版时间:2017
- 标注页数:1008页
- 文件大小:167MB
- 文件页数:1044页
- 主题词:飞机-金属复合材料-损伤(力学)-修理
PDF下载
下载说明
飞机金属结构复合材料修理技术PDF格式电子书版下载
下载的文件为RAR压缩包。需要使用解压软件进行解压得到PDF格式图书。建议使用BT下载工具Free Download Manager进行下载,简称FDM(免费,没有广告,支持多平台)。本站资源全部打包为BT种子。所以需要使用专业的BT下载软件进行下载。如BitComet qBittorrent uTorrent等BT下载工具。迅雷目前由于本站不是热门资源。不推荐使用!后期资源热门了。安装了迅雷也可以迅雷进行下载!
(文件页数 要大于 标注页数,上中下等多册电子书除外)
注意:本站所有压缩包均有解压码: 点击下载压缩包解压工具
图书目录
第1章 绪论与评述1
1.1 本书目的1
1.2 飞机结构的检查与修理类别1
1.2.1 飞机结构的设计与取证2
1.2.2 老龄飞机金属结构件的若干问题2
1.3 修理要求4
1.3.1 修理等级4
1.4 修理方法5
1.5 胶结修理实例5
1.6 复合材料补片与金属补片7
1.7 应用范围8
1.8 胶结和螺钉连接的试验比较9
1.9 研发要求11
1.10 结论13
参考文献13
第2章 材料选择与工程应用15
2.1 引言15
2.1.1 影响黏结的因素15
2.2 补片与增强件使用的材料16
2.2.1 金属材料17
2.2.2 非金属材料18
2.2.3 补片材料的选择20
2.3 胶黏剂体系21
2.3.1 胶黏剂的类型21
2.3.2 胶黏剂的性能22
2.3.3 胶黏剂的选择22
2.4 底胶和偶联剂24
2.5 胶黏剂和复合材料试验方法25
2.6 材料工程考虑26
2.6.1 残余应力26
2.6.2 固化压力与空隙27
2.6.3 挤出的胶带27
2.6.4 智能补片修理28
参考文献29
第3章 表面处理与胶结修理30
3.1 引言30
3.1.1 表面能与浸润30
3.1.2 黏结面加压与胶黏剂固化31
3.1.3 胶结性能31
3.1.4 胶结的标准和环境32
3.2 力学试验33
3.2.1 载荷与破坏模式33
3.2.2 胶结程序和性能的合格鉴定33
3.3 标准试验34
3.3.1 楔子耐久性试验34
3.3.2 断裂力学与劈裂试件34
3.4 胶结耐久性的基本原理35
3.4.1 表面粗糙度与胶结耐久性35
3.4.2 表面水合作用与胶结耐久性37
3.4.3 表面污染与胶结耐久性37
3.4.4 胶结耐久性模型38
3.5 表面准备的要求41
3.5.1 脱脂41
3.5.2 打磨、喷砂或浸蚀42
3.5.3 高能表面氧化层的形成43
3.5.4 偶联剂44
3.5.5 胶结底胶45
3.5.6 干燥46
3.6 胶黏剂的使用46
3.6.1 黏结面厚度的控制要素47
3.6.2 空穴的形成和极小化47
3.7 表面处理的质量控制48
3.7.1 水膜残迹测试48
3.7.2 表面功函数法48
3.7.3 傅立叶变换红外线分光镜48
3.7.4 光学反射率48
3.7.5 过程控制试片49
3.7.6 从业者的教育、技能和标准49
3.8 铝黏结体的表面准备49
3.8.1 工厂的处理过程49
3.8.2 飞机上的酸阳极化及酸浸蚀过程51
3.9 钛黏结体的表面准备53
3.9.1 工厂的处理过程54
3.9.2 飞机上的处理过程55
3.10 钢黏结体的表面准备55
3.10.1 工厂的处理过程56
3.10.2 飞机上的处理过程56
3.11 热固性基体复合材料的表面准备56
3.12 表面准备的近期研究58
3.12.1 胶结的溶胶-凝胶体技术58
3.12.2 胶结的热溶液处理59
参考文献59
第4章 胶黏剂的表征及其数据库67
4.1 引言67
4.2 通用的美国材料试验标准(ASTM)与美国军用技术规范(MIL)试验68
4.2.1 应力—应变许用值68
4.3 疲劳载荷72
4.4 断裂力学许用值72
4.4.1 静力载荷73
4.4.2 Ⅰ型模式73
4.4.3 Ⅱ型与混合模式73
4.4.4 疲劳载荷73
4.5 FM73数据库75
4.5.1 剪应力—应变许用值75
4.5.2 屈服准则76
4.5.3 玻璃化转变温度76
4.5.4 Fickean的吸湿扩散系数76
4.5.5 Ⅰ型断裂韧性77
参考文献78
第5章 常规胶结接头的疲劳试验80
5.1 引言80
5.1.1 胶结修理区内的损伤容限区域80
5.1.2 常规设计和认证过程81
5.2 双搭接接头疲劳试件(DOFS)81
5.2.1 DOFS的应力状态82
5.2.2 试验方法83
5.2.3 试验结果84
5.3 蒙皮加强片试件88
5.3.1 蒙皮加强片试件的应力状态89
5.3.2 试验方法及结果93
5.3.3 断裂力学方法96
5.4 讨论96
参考文献97
第6章 基于断裂力学的胶结修理体系环境影响评估99
6.1 引言99
6.2 材料与试件99
6.2.1 胶结的材料体系和制造99
6.3 试验方法100
6.3.1 试验前环境调试101
6.3.2 试验方法101
6.4 分析102
6.5 结果与讨论102
6.5.1 断裂韧性102
6.5.2 疲劳行为103
6.6 总结104
参考文献105
第7章 复合材料修理设计的解析方法107
7.1 引言107
7.2 公式与符号108
7.3 胶结增强件的载荷传递110
7.4 对称修理112
7.4.1 阶段Ⅰ:异物模拟112
7.4.2 阶段Ⅱ:应力强度因子114
7.4.3 塑性胶层116
7.4.4 有限裂纹尺寸117
7.4.5 有限元验证120
7.5 剪切模式120
7.6 单侧修理121
7.6.1 几何线性分析122
7.6.2 裂纹桥接模型125
7.6.3 几何非线性分析126
7.7 胶层固化形成的残余热应力130
7.7.1 温度分布130
7.7.2 局部加热引起的残余应力131
7.7.3 固化并冷却后的残余应力132
7.7.4 均匀温度变化引起的热应力133
7.7.5 验证133
参考文献134
第8章 裂纹胶结修理技术罗斯封闭形式解析解的新近扩充137
8.1 引言137
8.1.1 罗斯使用夹杂物模型建立的应力场138
8.1.2 罗斯的裂纹尖端应力强度因子解K139
8.2 各向同性补片的通用效率曲线图141
8.3 八边形和椭圆形补片形状之间的等效142
8.4 补片斜削对胶层应力的影响143
8.5 关于腐蚀影响的通用曲线145
8.6 补偿腐蚀损伤的补片设计147
8.7 覆盖加筋板裂纹的补片分析148
8.8 避免裂纹起裂的设计149
8.9 正交异性补片的通用效率曲线151
8.10 残余热应力对胶结修理的影响152
8.11 胶层非线性和脱胶对裂纹尖端应力强度因子的影响154
8.12 单侧补片的面外弯曲效应156
8.13 封闭形式分析面临的挑战157
8.14 结语157
参考文献158
第9章 数值分析与设计160
9.1 分析与设计160
9.2 二维有限元分析的公式描述160
9.2.1 单元刚度矩阵162
9.2.2 飞机机翼蒙皮裂纹的修理163
9.3 初始设计指南166
9.4 无肋加筋板的试验结果对比174
9.5 厚截面的修理175
9.5.1 试验结果177
9.6 主结构中孔边裂纹的修理179
9.7 开裂耳片的修理181
9.7.1 数值分析182
9.7.2 试验测试183
9.7.3 讨论184
9.8 交互作用表面裂纹的修理185
9.9 材料非线性186
9.9.1 胶结接头修理的控制微分方程187
9.10 变胶层厚度的影响192
9.11 在双轴载荷下带裂纹孔的修理197
9.12 关于厚截面修理的发现200
9.12.1 三维修理分析商业有限元程序的比较202
参考文献203
第10章 胶结修理的形状优化206
10.1 引言206
10.1.1 基于有限元的形状优化206
10.1.2 有限元模型化考虑207
10.1.3 本章概述207
10.2 改善补片斜削区分级的解析公式207
10.2.1 对称分级补片的一般构型208
10.2.2 单级情况的分析209
10.2.3 多级补片的分析209
10.2.4 第一级最优长度的估计210
10.2.5 随补片长度改变的最大剪应变最小限值210
10.2.6 随第一级刚度改变的最大剪应变下限211
10.2.7 数值实例211
10.2.8 讨论213
10.3 胶层应力和板件应力集中的有限元分析214
10.3.1 构型与有限元分析方法214
10.3.2 无胶带情况的结果216
10.3.3 有胶带情况的结果217
10.3.4 结果讨论218
10.4 对厚度方向形状进行优化的非梯度有限元方法219
10.5 接头厚度方向形状优化的有限元敏感度方法221
10.5.1 初始的几何形状、材料和载荷布置221
10.5.2 最优化方法221
10.5.3 基于铝补片修理对称裂纹的分析223
10.5.4 硼/环氧补片非对称裂纹修理的分析225
10.6 F/A-18飞机隔框增强件的厚度方向形状优化226
10.6.1 初始几何形状、材料及载荷布置227
10.6.2 增强件优化分析的参数227
10.6.3 最优增强件设计的应力结果229
10.6.4 讨论231
10.7 F/A-18飞机副翼铰链增强件的最优化231
10.7.1 初始的几何形状、材料和载荷布置231
10.7.2 结构增强以前的形状优化232
10.7.3 增强件的迭代设计233
10.7.4 讨论234
10.8 面内形状的影响235
10.8.1 几何形状、载荷及模型考虑236
10.8.2 用有限元输出结果确定Kt236
10.8.3 单轴载荷及2:1长宽比的补片237
10.8.4 单轴载荷及其他长宽比的补片237
10.8.5 带孔板的模拟238
10.8.6 单轴受载板在补片中心的应力降低量238
10.8.7 结果综述与讨论238
10.9 结论238
参考文献239
第11章 热应力分析242
11.1 引言242
11.2 加热导致的圆板初始应力解析表达式242
11.2.1 有限元结果与解析结果的比较246
11.2.2 正交异性解249
11.2.3 一维片条内的热应力250
11.2.4 剥离应力252
11.2.5 层压板的热膨胀系数252
11.3 有限元热应力分析254
11.3.1 二维片条接头255
11.3.2 三维片条接头257
11.4 飞机机翼大型修理应用情况的热应力分析258
11.4.1 有限元分析259
11.4.2 边界约束系数263
11.5 结束语264
附录265
参考文献265
第12章 修理结构的裂纹扩展分析267
12.1 引言267
12.2 修理结构的裂纹闭合分析267
12.2.1 小范围屈服267
12.2.2 稳态裂纹的大范围屈服解270
12.2.3 大范围屈服条件下塑性导致的裂纹闭合272
12.3 超载效应及有限元验证273
12.4 残余热应力及与试验结果的对比277
12.4.1 残余热应力277
12.4.2 谱载作用下的试验结果279
12.5 结束语282
参考文献282
第13章 硼/环氧修理效率研究284
13.1 引言284
13.2 修理后裂纹的应力强度分析284
13.2.1 应力强度模型284
13.2.2 裂纹扩展评估286
13.2.3 考虑脱胶损伤扩展的情况286
13.3 试验方法287
13.4 疲劳研究288
13.4.1 补片内的脱胶损伤288
13.4.2 应力幅值的影响289
13.4.3 补片厚度的影响291
13.4.4 R的影响291
13.4.5 温度的影响293
13.4.6 板厚变化的影响294
13.4.7 修理后板件的剩余强度296
13.5 硼/环氧补片的设计方法298
13.5.1 循环载荷298
13.5.2 谱载荷300
13.5.3 检查剩余强度301
参考文献301
第14章 GLARE材料修理效率研究303
14.1 引言303
14.1.1 纤维金属层压板概述与背景303
14.2 不同补片材料的参数研究304
14.3 试验结果309
14.4 讨论312
14.5 结论313
参考文献313
第15章 石墨/环氧补片修理效率研究315
15.1 引言315
15.2 薄蒙皮构件的修理315
15.3 厚截面的修理317
15.4 石墨/环氧与硼/环氧补片321
15.5 黏结面缺陷的影响324
15.6 冲击损伤的影响328
15.7 服役温度的影响329
15.8 湿-热环境的影响330
15.9 战伤修理331
15.10 今后的工作332
15.11 感谢333
参考文献333
第16章 多处损伤的修理335
16.1 引言335
16.2 试件与载荷335
16.2.1 波音搭接接头335
16.2.2 “空客”搭接接头338
16.3 修理339
16.3.1 修理原理339
16.3.2 修理细节340
16.4 应力分析341
16.4.1 热-弹性分析341
16.4.2 有限元分析342
16.5 疲劳试验结果345
16.5.1 未修理的基准机身搭接接头345
16.5.2 增强的基准机身搭接接头试件348
16.5.3 修理的环境评估349
16.5.4 湿-热环境350
16.5.5 NaCl水溶液350
16.6 试件的损伤容限评估351
16.6.1 胶层脱胶351
16.6.2 冲击损伤352
16.6.3 拉伸试验354
16.7 全尺寸修理验证355
16.7.1 空客A330和A340疲劳试件355
16.7.2 波音727、波音747和波音767飞行验证356
16.7.3 加强板的检查358
16.7.4 验证小结358
16.8 结论359
参考文献360
第17章 用于民机修理的复合材料加强片损伤容限评估363
17.1 引言363
17.1.1 损伤容限与断裂控制363
17.1.2 断裂控制计划365
17.2 复合材料加强片的损伤容限试验366
17.3 符合性检查和FAA监督368
17.3.1 试片构型368
17.3.2 试件说明369
17.3.3 铝母板内的裂纹制备370
17.3.4 表面处理和复合材料加强片的安装371
17.3.5 对复合材料试片制造冲击损伤371
17.3.6 湿-温度浸润371
17.3.7 层压板-铝板的刚度比371
17.3.8 试验过程与设备372
17.3.9 含静态应变测量的疲劳试验373
17.3.10 静力拉伸极限强度试验373
17.4 试验结果373
17.4.1 疲劳试验373
17.4.2 应变场的测量378
17.5 结论384
17.5.1 结果的推广应用384
17.5.2 考虑检查要求的损伤容限评估384
参考文献385
第18章 修理板件应力强度预估模型的验证387
18.1 引言387
18.2 K应变计388
18.2.1 K应变计的公式388
18.3 用应变计进行KI测量的原理389
18.3.1 Westergaard方程389
18.3.2 关于应力强度因子的罗斯夹杂模型389
18.3.3 Wang的裂纹桥接模型390
18.4 试验程序390
18.5 应变测量392
18.5.1 未修理试件392
18.5.2 修理试件393
18.6 裂纹长度393
18.7 时间依变特性395
18.8 结论396
18.9 术语397
参考文献397
第19章 声疲劳裂纹的胶结修理398
19.1 引言398
19.2 开裂经历399
19.2.1 进气短舱399
19.2.2 后机身开裂401
19.3 声压水平401
19.3.1 进气短舱401
19.3.2 后机身402
19.3.3 功率谱密度402
19.4 随机响应分析402
19.5 应力强度因子402
19.6 开裂短舱进气口的有限元分析403
19.6.1 裂纹扩展研究404
19.6.2 对修理破坏研究的概括409
19.7 对裂纹板的高阻尼修理409
19.7.1 高阻尼补片的设计409
19.7.2 高阻尼补片的阻尼409
19.7.3 修理后含裂纹板件的分析412
19.7.4 结果与讨论413
19.8 后机身有限元模型416
19.8.2 声疲劳裂纹扩展数据417
19.8.3 残余热应力419
19.8.4 阻尼数据419
19.8.5 胶黏剂数据420
19.9 F/A-18飞机的热环境421
19.10 分析结果421
19.11 试验422
19.12 关于后机身修理的结论424
参考文献424
第20章 智能补片系统427
20.1 引言427
20.2 智能补片方法429
20.3 损伤检测研究432
20.3.1 载荷传输(应变)技术432
20.3.2 残余应变技术439
20.3.3 电-机阻抗、传递函数和应力波技术442
20.3.4 胶结退化传感器445
20.4 智能补片实验室概念验证件448
20.5 飞行验证机450
20.5.1 有限元分析——损伤传感技术451
20.5.2 健康监控系统453
20.6 结论456
参考文献456
第21章 满足现航空工业认证规程安全要求的胶结修理459
21.1 引言459
21.2 胶结修理的认证460
21.2.1 修理的认证要求460
21.2.2 胶结修理460
21.2.3 管理缺陷461
21.3 修理设计信息462
21.3.1 现有的要求462
21.3.2 补充463
21.4 试验分析与发展463
21.4.1 设计许用值463
21.4.2 静力分析466
21.4.3 疲劳与损伤容限分析469
21.4.4 研发试验473
21.5 全尺寸试验474
21.5.1 现有要求474
21.6 服役中的管理与检查474
21.6.1 现有要求474
21.6.2 补充474
21.7 胶结修理认证的发展趋势475
21.8 结论475
参考文献475
第22章 关键修理的认证479
22.1 含裂纹结构修理现状479
22.2 修理的疲劳问题480
22.2.1 疲劳对修理效率的影响480
22.2.2 补片修理疲劳许用值481
22.2.3 补片修理分析验证482
22.3 修理的环境耐久性问题484
22.3.1 补片修理的环境耐久性保证484
22.3.2 澳大利亚关于服役耐久性的经验486
22.4 “智能补片”487
22.5 讨论488
22.6 结论489
参考文献490
第23章 金属飞机结构复合材料胶结修理的无损评估与质量控制492
23.1 引言492
23.1.1 NDI要求与损伤容限493
23.1.2 NDI的评定494
23.2 分层、脱胶和胶结破坏的检测495
23.2.1 脉冲反射超声技术496
23.2.2 透射式超声技术506
23.2.3 导波506
23.2.4 谐振试验检测方法508
23.2.5 热成像技术510
23.2.6 其他技术513
23.3 复合材料加强件下母体材料内裂纹的检测516
23.3.1 涡流检测516
23.3.2 X射线照相检测521
23.3.3 裂纹监控的挑战523
23.4 服役使用中的质量控制问题530
23.4.1 质量保证530
23.4.2 实际标定标准的使用531
23.5 结论534
参考文献537
第24章 胶结修理的实用技术541
24.1 引言541
24.1.1 修理技术的管理543
24.2 修理应用技术543
24.2.1 材料选择543
24.2.2 表面准备544
24.2.3 飞机上修理的加热程序551
24.2.4 修理部分的压力施加555
24.3 职业保健与安全557
24.3.1 溶剂558
24.3.2 砂打磨558
24.3.3 纤维558
24.3.4 可对飞机造成的危险558
24.4 质量管理559
24.5 设施560
24.6 训练与资格认证560
24.7 不良修理概念561
24.8 结论562
参考文献562
第25章 快速应用技术:飞机战伤修理566
25.1 引言566
25.2 飞机战伤修理567
25.2.1 战伤567
25.2.2 ABDR标准567
25.2.3 ABDR的类型568
25.3 金属机械紧固修理与复合材料胶结修理在ABDR中的对比569
25.3.1 复合材料胶结修理按战伤情况的改造569
25.3.2 复合材料层压树脂和胶黏剂570
25.3.3 纤维570
25.3.4 用于ABDR的简化设计方法570
25.3.5 表面处理571
25.3.6 复合材料胶结补片的成形571
25.3.7 机械连接的金属修理571
25.3.8 试件的疲劳与静力试验572
25.3.9 试验结果比较572
25.4 胶结复合材料飞机战伤修理系统的建立573
25.4.1 树脂的开发574
25.4.2 修理的耐久性、强度与表面处理574
25.4.3 力学性能576
25.5 DSTO/ABDR系统的应用577
25.5.1 树脂的计量、混合与配方577
25.5.2 预先建成表面处理方法578
25.5.3 修理固化与实施578
25.5.4 加热程序578
25.5.5 真空模塑工具578
25.6 结论579
参考文献580
第26章 胶结修理技术人员的标准化训练与资格认证583
26.1 引言583
26.1.1 改善训练与过程控制的效益——实例583
26.2 当前的任务——通用方法583
26.2.1 标准化的优点583
26.2.2 建立一个可靠的修理数据库——“我们彼此全都在其中”584
26.3 当前的训练与资格认证方法584
26.4 正式的行业结构585
26.4.1 行业结构的目标585
26.4.2 一种四级行业结构——ARTI模式585
26.5 ARTI模式对胶结修理专业人员的训练586
26.6 胶结修理专业人员的资格认证588
26.6.1 波音楔子试验(BWT)——一种可以接受的标准588
26.6.2 认证试验的管理591
26.7 结论592
参考文献592
第27章 历史案例:F-111飞机机翼下蒙皮修理593
27.1 引言593
27.2 裂纹位置与剩余强度593
27.3 修理的实例化要求595
27.3.1 设计载荷情况595
27.3.2 疲劳载荷595
27.4 验证策略596
27.5 设计验证(有限元分析)596
27.5.1 无裂纹、未修理机翼模型596
27.6 包括热效应的含裂纹补片修理模型597
27.7 修理实例化(典型试件试验)599
27.7.1 典型胶结接头599
27.7.2 板试件599
27.8 盒形试件602
27.9 修理历史603
27.10 结论603
参考文献603
第28章 历史案例:安装在L-1011民用飞机上的复合材料加强件605
28.1 引言605
28.2 机身舱门环绕结构试验606
28.2.1 全尺寸结构试验原理606
28.2.2 L-1011机身结构606
28.2.3 用复合材料加强件修理机身试验件606
28.2.4 双轴试验装置介绍608
28.3 机身舱门环绕结构的试验结果609
28.3.1 安装复合材料加强件前的结构试验609
28.3.2 安装复合材料加强件后的结构试验610
28.3.4 有限元分析结果的验证614
28.3.5 无损检测614
28.4 构件级试验:舱门拐角试件615
28.4.1 舱门拐角试验概述615
28.4.2 小尺寸的舱门拐角试验结果616
28.5 L-1011飞机复合材料加强件的安装619
28.5.1 L-1011飞机旅客舱门的复合材料加强件修理619
28.5.2 舱门环绕结构及复合材料加强件的无损检测621
28.5.3 L-1011飞机的检测间隔623
28.5.4 质量保证措施624
28.6 FAA和工业界的承认与批准625
28.7 结论625
参考文献626
第29章 历史案例:F-111飞机机翼转枢接头区的增强628
29.1 引言628
29.2 加强件设计629
29.3 材料选择与评定631
29.4 增强系统的选择与评定632
29.4.1 力学试验评定632
29.4.2 固化特征与成形性研究632
29.4.3 胶黏剂的选择与评定633
29.4.4 表面处理程序的选择与评定634
29.4.5 加强件系统的修正634
29.4.6 残余应力的极小化634
29.5 加强件应用技术634
29.5.1 温度634
29.5.2 压力635
29.6 加强件的适配问题635
29.7 机队飞机的适配问题636
29.8 结论637
参考文献637
第30章 历史案例:F/A-18飞机Y470.5中央机身隔框的胶结复合材料增强639
30.1 引言639
30.1.1 背景639
30.2 隔框的有限元分析与增强640
30.2.1 隔框有限元分析的结果640
30.2.2 胶层中沿厚度方向应力的测量642
30.3 典型试件(弯曲梁试件)的有限元设计642
30.4 试验计划642
30.4.1 弯曲梁试件的静力试验642
30.4.2 弯曲梁试件的耐久性试验644
30.4.3 疲劳后的剩余强度644
30.5 全尺寸疲劳试件试装增强件644
30.6 讨论644
30.6.1 实施ECP前的增强644
30.6.2 实施ECP后的增强645
30.7 结论646
参考文献646
第31章 C-5A飞机机身顶部裂纹648
31.1 引言648
31.2 损伤容限分析648
31.3 修理选项650
31.3.1 补片材料的刚度650
31.3.2 热膨胀系数650
31.4 胶结修理设计651
31.4.1 用CalcuRep计算所有载荷情况651
31.4.2 补片与结构的适配653
31.4.3 补片的制造653
31.5 修理裂纹的有限元模型654
31.6 结论658
参考文献658
第32章 历史案例:F-16飞机燃油透气孔修理659
32.1 引言659
32.2 损伤容限分析659
32.3 修理方案选择661
32.4 胶结修理设计662
32.4.1 运行温度663
32.4.2 最大运行温度663
32.4.3 累积温度663
32.5 试验664
32.5.1 铝加强件的疲劳分析664
32.6 胶结修理664
32.6.1 修理安装程序666
32.7 结论667
参考文献667
第33章 F/A-18飞机整流罩内的副翼铰链增强修理668
33.1 引言668
33.2 载荷情况669
33.3 设计与应力分析669
33.4 静力试验与修理验证673
33.5 认证及飞机上的实现675
33.6 结论675
参考文献675
第34章 英国的应用情况677
34.1 引言677
34.2 设计研究677
34.3 英国皇家空军飞机的修理679
34.3.1 次要结构修理679
34.3.2 主要结构修理680
34.3.3 鸟撞防护680
34.4 EH 101飞机机体结构全尺寸疲劳试件修理680
参考文献684
第35章 历史案例:DC-10/MD-11飞机的修理应用686
35.1 引言686
35.2 支持在飞机上安装应用的修理发展与验证任务686
35.2.1 修理设计686
35.3 修理分析689
35.4 修理设计的验证690
35.5 无损检测696
35.6 DC-10/MD-11商用飞机修理的目前状态697
第36章 历史案例:CF-116飞机机翼上蒙皮的硼加强件疲劳增强699
36.1 引言699
36.2 背景699
36.2.1 压缩导致的疲劳裂纹700
36.3 修理考虑701
36.4 复合材料胶结加强件702
36.5 加强件的设计与分析702
36.6 加强件的制造与安装程序706
36.6.1 加强件合格性试验707
36.7 加强件的金属断面显微镜观察分析709
36.8 机队的经验712
36.9 讨论713
36.10 结论713
36.11 复合材料修理经验714
参考文献714
附录A材料性能715
第37章 复合材料胶结修理的服役耐久性——商业验证项目717
37.1 引言717
37.2 验证机的加强件718
37.2.1 QANTAS的验证项目718
37.2.2 安捷的龙骨梁增强719
37.3 服役环境和修理位置719
37.3.1 温度719
37.3.2 外物损伤720
37.3.3 气流与侵蚀720
37.3.4 飞机燃油、液压油及润滑剂720
37.3.5 其他问题721
37.4 胶结耐久性与表面处理721
37.5 案例研究结果722
37.5.1 QANTAS项目722
37.5.2 安捷飞机龙骨梁的验证机增强725
37.6 讨论与经验725
37.6.1 使用保护层进行侵蚀防护726
37.6.2 修理位置与设计726
37.6.3 验证项目的适用性726
37.7 结论726
参考文献727
第38章 历史案例:CH-47飞机吊货钩梁的复合材料胶结修理728
38.1 引言728
38.2 缺陷描述728
38.3 方法证明728
38.3.1 载荷分析729
38.3.2 设计载荷729
38.3.3 静强度分析730
38.3.4 疲劳分析731
38.3.5 验证试验731
38.4 补片系统与环境保护731
38.5 修理程序732
38.6 连续适航性/检测732
参考文献734
第39章 历史案例:大型胶结增强件修理技术735
39.1 背景735
39.2 应用实例735
39.2.1 全长度的旋翼叶片加强件735
39.2.2 大型机翼增强735
39.2.3 大型机身增强736
39.3 当前技术状态736
39.3.1 胶结过程的极限状态736
39.3.2 喷砂/硅烷过程的步骤737
39.4 处理区域的适用性738
39.4.1 溶剂清洗步骤738
39.4.2 喷砂步骤738
39.4.3 加热方法739
39.5 生产环境下的大型修理739
39.6 结论744
参考文献744
第40章 历史案例:T-38飞机机翼下蒙皮复合材料补片增强修理745
40.1 引言745
40.2 验证试验745
40.2.1 试件描述745
40.2.2 复合材料增强件的制造与胶结748
40.2.3 应变片布置748
40.2.4 试验谱与试验设备748
40.3 试验结果749
40.3.1 应变计测量结果749
40.3.2 裂纹扩展结果750
40.4 试验结果与分析预测结果的比较751
40.5 将复合材料增强修理用于全尺寸机翼试验753
40.6 结论754
参考文献754
第41章 案例历史:美国空军C-141和C-130飞机的先进复合材料修理755
41.1 背景755
41.2 修理设计757
41.3 补片安装技术的发展759
41.4 工业化与修理760
41.5 成功与失败761
41.6 其他应用情况763
41.6.1 C-141飞机763
41.6.2 C-130飞机764
41.6.3 现场修理765
41.7 费用节省766
41.8 其他研究767
41.8.1 加强件设计优化767
41.8.2 高压缩载荷767
41.8.3 腐蚀修理767
41.8.4 大长宽比修理768
41.8.5 承力框架修理768
41.8.6 机身蒙皮修理769
41.9 经验总结770
41.10 综述772
参考文献772
第42章 案例历史:船舶结构的复合材料胶结修理774
42.1 引言774
42.2 材料发展与表征776
42.3 复合材料增强件的安装780
42.4 增强效率的评估781
42.5 服役性能782
42.6 技术改进784
42.7 目前状态——2000年785
42.8 结论785
参考文献785
附录1 基于损伤容限理念的飞机修理787
附1.0 摘要787
附1.1 引言787
附1.2 修理引起的结构性能的降低788
附1.3 修理后结构的寿命改善794
附1.4 可检性的改善799
附1.5 铆接的质量801
附1.6 修理引起的可检性降低806
附1.7 修理的损伤容限评估808
附1.7.1 简化裂纹扩展方法的建立809
附1.7.2 特定修理的裂纹扩展评估815
附1.7.3 今后可能的方法816
附1.8 结论818
附1.9 对修理结构的基本要求818
参考文献819
附录2 大型飞机机体结构损伤容限修理设计技术820
附2.1 引言820
附2.2 静力模式820
附2.2.1 修理补片许用值和安全裕度820
附2.2.2 紧固连接件许用值和安全裕度821
附2.2.3 安全裕度822
附2.2.4 修理的刚度校核822
附2.2.5 修理的紧固件弯曲校核823
附2.2.6 关于铆钉间屈曲指导原则823
附2.3 损伤容限模式823
附2.3.1 裂纹扩展分析823
附2.3.2 剩余强度评估834
附2.3.3 检测门槛值和间隔834
附2.4 常规修理834
附2.4.1 贴近修理835
附2.4.2 加筋件处的修理835
附2.4.3 圆形修理835
附2.5 计算分析程序RAPID-FEM及门框开口的修理835
附2.5.1 计算分析程序RAPID-FEM835
附2.5.2 舱门开口处的修理835
附2.6 分析方法流程图836
参考文献837
附录A 紧固件载荷传递的二维分析837
附录B 应力强度因子解878
附录C 通用载荷/应力谱的编制885
附录D 一次循环当量应力计算911
附录E 贴近修理916
附录F 加筋件处的修理924
附录G 圆形修理937
附录H RAPID-FEM程序944
附录I RAPID-FEM程序开发及含一个舱门开口的机身结构三维分析959
附录J 三个带门开口机身段的应力分析990
附录K 天线安装999
热门推荐
- 1111710.html
- 3022036.html
- 2807678.html
- 1230862.html
- 2809612.html
- 1709025.html
- 1964516.html
- 3684910.html
- 23737.html
- 583966.html
- http://www.ickdjs.cc/book_3002569.html
- http://www.ickdjs.cc/book_451995.html
- http://www.ickdjs.cc/book_2411259.html
- http://www.ickdjs.cc/book_1485789.html
- http://www.ickdjs.cc/book_2545928.html
- http://www.ickdjs.cc/book_197164.html
- http://www.ickdjs.cc/book_1355450.html
- http://www.ickdjs.cc/book_2441759.html
- http://www.ickdjs.cc/book_1535551.html
- http://www.ickdjs.cc/book_1831163.html